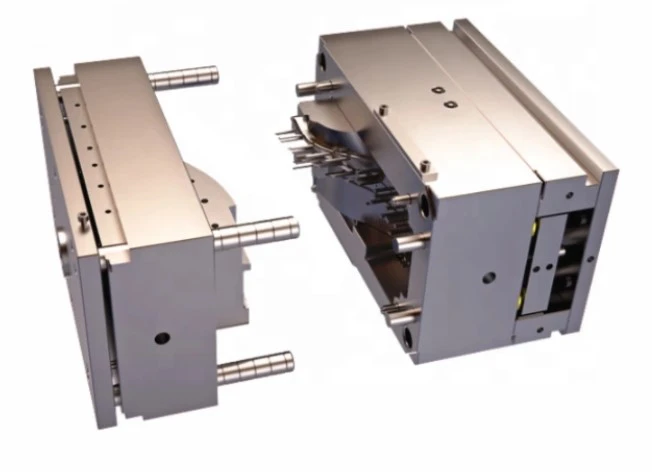
Thiết kế khuôn ép phun là một trong nhóm dịch vụ được Plasticsaigon chúng tôi ưu tiên tập trung nguồn lực để có giá tốt nhất
Cơ bản về thiết kế khuôn ép phun
Việc tuân theo một số quy tắc cơ bản về thiết kế chi tiết đúc phun sẽ tạo ra các chi tiết dễ sản xuất và lắp ráp hơn, và thường bền hơn nhiều khi sử dụng.
Giới thiệu về ép phun
Thiết kế các bộ phận bằng nhựa là một nhiệm vụ phức tạp liên quan đến nhiều yếu tố giải quyết các yêu cầu ứng dụng. “Bộ phận sẽ được sử dụng như thế nào?” “Nó phù hợp với các bộ phận khác trong cụm lắp ráp như thế nào?” “Nó sẽ chịu tải trọng nào khi sử dụng?” Ngoài các vấn đề về chức năng và cấu trúc, các vấn đề về gia công đóng vai trò lớn trong thiết kế bộ phận nhựa đúc phun. Cách nhựa nóng chảy đi vào, lấp đầy và làm mát bên trong khoang để tạo thành bộ phận phần lớn quyết định hình dạng các đặc điểm trong bộ phận đó phải có. Việc tuân thủ một số quy tắc cơ bản về thiết kế bộ phận đúc phun sẽ tạo ra một bộ phận, ngoài việc dễ sản xuất và lắp ráp hơn, thường sẽ mạnh hơn nhiều khi sử dụng. Chia một bộ phận thành các nhóm cơ bản sẽ giúp bạn xây dựng bộ phận của mình theo cách hợp lý đồng thời giảm thiểu các vấn đề về đúc. Khi phát triển một bộ phận, hãy luôn ghi nhớ cách đúc bộ phận đó và những gì bạn có thể làm để giảm thiểu ứng suất.
Ứng dụng ép phun
Ép phun nhựa là quy trình được ưa chuộng để sản xuất các bộ phận bằng nhựa. Ép phun được sử dụng để tạo ra nhiều thứ như vỏ điện tử, hộp đựng, nắp chai, nội thất ô tô, lược và hầu hết các sản phẩm nhựa khác hiện có. Nó lý tưởng để sản xuất khối lượng lớn các bộ phận bằng nhựa do thực tế là có thể sản xuất nhiều bộ phận trong mỗi chu kỳ bằng cách sử dụng khuôn ép phun nhiều khoang. Một số ưu điểm của ép phun là độ chính xác dung sai cao, khả năng lặp lại, lựa chọn vật liệu lớn, chi phí nhân công thấp, tổn thất phế liệu tối thiểu và ít cần hoàn thiện các bộ phận sau khi đúc. Một số nhược điểm của quy trình này là đầu tư dụng cụ ban đầu đắt đỏ và hạn chế về quy trình.
Các ứng dụng bao gồm:
-
- Bao bì
- Hàng tiêu dùng
- Thiết bị y tế
- Điện tử và viễn thông
- Các bộ phận cơ khí (bao gồm cả bánh răng)
- Hầu hết các sản phẩm nhựa thông thường khác hiện có ngày nay
Câu chuyện của khách hàng
Trước
Plasticsaigon tiết kiệm tới 20% thời gian giao khuôn với phần mềm Cimatron
Xưởng chế tạo khuôn mẫu và gia công tùy chỉnh sử dụng phần mềm CAD/CAM tích hợp để hợp tác thiết kế ngay từ đầu với khách hàng về các công cụ phức tạp, có dung sai chặt chẽ hơn….
Plasticsaigon loại bỏ lỗi và giảm 50% thời gian thiết kế với phần mềm Cimatron
Xưởng sản xuất khuôn ép phun sử dụng phần mềm CAD/CAM tích hợp để thiết kế và sản xuất các mẫu thử nghiệm và dụng cụ sản xuất phức tạp, có độ dung sai cao, tùy chỉnh….
Plasticsaigon cung cấp khuôn ép phun chất lượng cao nhanh gấp đôi với phần mềm Cimatron
Phần mềm CAD/CAM tích hợp giúp nhà sản xuất khuôn mẫu duy trì lợi thế cạnh tranh bằng cách rút ngắn thời gian tạo mẫu và sản xuất khuôn mẫu….
Kế tiếp
Những điều cơ bản về ép phun
Thuật ngữ ép phun >>
Boss: Chỉ các phần nhô tròn trên các bộ phận nhựa và khuôn mẫu (#2 trong Hình 1 bên dưới)
Khoang Chỉ: nửa trên của khuôn ép phun thường là bề mặt hiển thị của sản phẩm hoàn thiện nhưng chủ yếu là lõm
Lõi Chỉ: mặt của dụng cụ nơi phần nhựa được phun vào; còn được gọi là nửa dưới của dụng cụ
Core Outs: Chỉ phần của một bộ phận được cắt bỏ để đạt được độ dày thành đồng đều. Phần này của bộ phận không có chức năng sử dụng cuối cùng nào khác ngoài việc làm nhẹ bộ phận và giảm cong vênh
Bản nháp: Chỉ phần của bộ phận đúc phun có một số độ côn để dễ tháo ra khỏi khuôn. Nhìn chung, tất cả các thành phần nhựa nên được thiết kế với bản nháp khi có thể
Cổng: Chỉ nơi nhựa đi vào khoang khuôn. Có hai loại cổng như sau:
1. Cổng cắt tự động: Cổng tích hợp các tính năng trong công cụ để phá vỡ hoặc cắt cổng khi công cụ đúc được mở ra để đẩy bộ phận ra
2. Cổng cắt thủ công: Cổng yêu cầu người vận hành tách các bộ phận khỏi các thanh dẫn trong quá trình vận hành thứ cấp
Khu vực Gibbs: của khuôn ép phun tùy chỉnh giữ thanh trượt xuống để cam có thể kích hoạt nó
Tải bằng tay: Các đặc điểm nhôm hoặc thép trong khuôn được sử dụng để tạo các vết cắt ở các bộ phận đúc. Chúng được lấy ra khỏi khuôn bằng tay trong quá trình đẩy bộ phận ra.
Gót chân: Chỉ phần của khuôn ép phun tùy chỉnh tự động giữ cho thanh trượt ở vị trí phía trước khi máy ép khuôn đóng trên khuôn
Chốt sừng Chốt: dùng để kích hoạt thanh trượt trên khuôn ép phun tự động
Đường vẽ Hướng: mà hai nửa khuôn ép phun tùy chỉnh sẽ tách ra khỏi phần nhựa cho phép nó được đẩy ra mà không có bất kỳ vật cản nào từ kim loại tạo ra các vết cắt
Ribs: Chỉ các đặc điểm mỏng có lưỡi trên một phần được sử dụng để gia cố các phần tường và gờ. Ngoài ra, được sử dụng để giảm thiểu cong vênh (#3 trong Hình 1 bên dưới)
Đường dẫn: Một kênh cắt vào khuôn ép phun tùy chỉnh, trong đó nhựa đi từ máy ép phun, qua ống rót, qua đường dẫn và sau đó qua cổng cuối cùng là lấp đầy bộ phận
Cắt: là khi nhựa đi vào khuôn và sự nóng chảy được duy trì bằng ma sát do tốc độ và áp suất tạo ra. Cắt quá nhiều có thể khiến vật liệu nhựa bị cháy, cắt quá ít có thể khiến vật liệu đóng băng gây ra hiện tượng bắn ngắn
Bắn ngắn: Kết quả của một bộ phận nhựa không được lấp đầy hoàn toàn, bao gồm một số hoặc tất cả các chi tiết
Tỷ lệ co ngót: Chỉ mức độ vật liệu nhựa sẽ co lại sau khi làm mát. Tỷ lệ co ngót này được thêm vào bộ phận trước khi khuôn được thiết kế. Mỗi vật liệu nhựa có tỷ lệ co ngót riêng, từ .001 trên một inch đến .060 trên một inch. Mặc dù hầu hết nằm trong khoảng từ .004″ đến .021″
Thuật ngữ hành động bên: được sử dụng cho các slide và/hoặc kéo tay được sử dụng trong quá trình xây dựng khuôn ép phun
Dấu chìm: Chỉ các khu vực của bộ phận đúc mà nó có vẻ bị chìm xuống, do các phần thành không đồng nhất, các phần thành dày và tỷ lệ gờ/phần lồi so với độ dày không đúng
Khu vực trượt: của khuôn ép nhựa tùy chỉnh được sử dụng để tạo các vết cắt. Yêu cầu đối với khuôn ép tự động
Kênh phun: liên kết vòi phun của máy ép phun với ống dẫn
Steel Safe: Chỉ lượng kim loại còn lại trên khuôn để điều chỉnh kích thước. Ví dụ, nếu bạn có đường kính bên trong được cho là .500, bạn có thể để khuôn ở mức .505 trong trường hợp bạn bị co ngót quá mức
Đúc thành mỏng: Đúc các bộ phận bằng nhựa có độ dày thành từ 0,005″ đến 0,060″
Phần cắt dưới: Chỉ phần của thành phần được thiết kế mà cần phải trượt hoặc kéo bằng tay để tạo ra các lỗ, cửa sổ hoặc kẹp không nằm trên đường kéo (#1 trong Hình 1 bên dưới)
Vết tích Vật: liệu nhô ra khỏi khu vực cổng sau khi thanh trượt cổng đã được tháo ra khỏi bộ phận đúc phun. Vết tích này thường được cắt tỉa bởi người vận hành máy đúc
Độ dày: thành Chỉ độ dày của mặt cắt ngang của bộ phận nhựa
Cong: vênh là khu vực của một bộ phận đúc phun bị biến dạng trong quá trình làm mát hoặc đúc, gây ra kết quả không mong muốn trong sản phẩm hoàn thiện. Thường do các phần tường không đồng đều
- Các loại polyme phù hợp nhất cho ép phun
- Thiết bị ép phun
- Quy trình ép phun
- Chu trình ép phun
- Các loại quy trình ép phun khác nhau
- Nhấn mạnh
- Cổng
- Cổng chung
- Vị trí cổng
- Độ dày của tường
- Dấu chìm
- Kết cấu
- Đường phân chia
- Các lỗi đúc khuôn phổ biến
Các loại polyme phù hợp nhất cho ép phun
Có hàng chục ngàn vật liệu khác nhau có sẵn để đúc phun. Hầu hết các loại polyme có thể được sử dụng, bao gồm tất cả các loại nhựa nhiệt dẻo (như nylon, polyethylene và polystyrene) và một số chất đàn hồi. Các vật liệu được lựa chọn dựa trên độ bền và chức năng cần thiết cho bộ phận cuối cùng, nhưng mỗi vật liệu cũng có các thông số đúc khác nhau cần được xem xét. Việc trộn các vật liệu có sẵn với hợp kim hoặc hỗn hợp các vật liệu đã phát triển trước đó cho phép các nhà thiết kế sản phẩm lựa chọn từ nhiều loại vật liệu để tìm ra loại có đúng các đặc tính.
Thiết bị ép phun
Máy ép phun:
Máy ép phun, còn được gọi là máy ép, bao gồm một phễu chứa vật liệu, một xi lanh phun hoặc pít tông dạng vít và một bộ phận gia nhiệt. Khuôn được kẹp vào tấm ép của máy ép, tại đó nhựa được phun vào khuôn thông qua lỗ phun. Máy ép được đánh giá theo trọng tải, là phép tính về lượng lực kẹp mà máy có thể tạo ra. Lực này giữ cho khuôn đóng trong quá trình ép phun. Trọng tải có thể thay đổi từ dưới 5 tấn đến 6.000 tấn, mặc dù máy ép có trọng tải cao hơn hiếm khi được sử dụng. Tổng lực kẹp cần thiết được xác định bởi diện tích chiếu của bộ phận tùy chỉnh đang được đúc. Diện tích chiếu này được nhân với lực kẹp từ 2 đến 8 tấn cho mỗi inch vuông của các diện tích chiếu. Theo nguyên tắc chung, có thể sử dụng 4 hoặc 5 tấn/inch cho hầu hết các sản phẩm. Nếu vật liệu nhựa rất cứng, nó sẽ cần nhiều áp suất phun hơn để lấp đầy khuôn, do đó cần nhiều trọng tải kẹp hơn để giữ cho khuôn đóng. Lực cần thiết cũng có thể được xác định bởi vật liệu được sử dụng và kích thước của bộ phận, với các bộ phận nhựa lớn hơn đòi hỏi lực kẹp lớn hơn.
Khuôn:
Khuôn hoặc khuôn đúc là dụng cụ dùng để sản xuất các bộ phận nhựa trong quá trình đúc. Theo truyền thống, khuôn ép phun rất tốn kém để sản xuất và chỉ được sử dụng trong các ứng dụng sản xuất khối lượng lớn, nơi sản xuất hàng nghìn bộ phận. Khuôn thường được chế tạo từ thép đã tôi, thép đã tôi trước, nhôm và/hoặc hợp kim berili-đồng. Việc lựa chọn vật liệu để chế tạo khuôn chủ yếu là vấn đề kinh tế. Khuôn thép thường tốn kém hơn để chế tạo nhưng có tuổi thọ dài hơn, bù đắp cho chi phí ban đầu cao hơn so với số lượng bộ phận được tạo ra trước khi bị mòn nhiều hơn. Khuôn thép đã tôi trước có khả năng chống mài mòn kém hơn và chủ yếu được sử dụng cho các yêu cầu về khối lượng thấp hơn hoặc các thành phần lớn hơn. Độ cứng của thép đã tôi trước thường là 38 và 45 trên thang Rockwell-C. Khuôn thép đã tôi được xử lý nhiệt sau khi gia công, giúp chúng vượt trội về khả năng chống mài mòn và tuổi thọ. Độ cứng thông thường nằm trong khoảng từ 50 đến 60 Rockwell-C (HRC).
Khuôn nhôm có giá thành thấp hơn đáng kể so với khuôn thép, và khi nhôm cấp cao hơn như nhôm máy bay QC-7 và QC-10 được sử dụng và gia công bằng thiết bị vi tính hiện đại, chúng có thể tiết kiệm chi phí đúc hàng trăm nghìn bộ phận. Khuôn nhôm cũng có thời gian quay vòng nhanh và chu kỳ nhanh hơn do tản nhiệt tốt hơn. Chúng cũng có thể được phủ lớp chống mài mòn cho vật liệu gia cố sợi thủy tinh. Đồng berili được sử dụng ở những khu vực của khuôn cần loại bỏ nhiệt nhanh hoặc những khu vực phát sinh nhiệt cắt nhiều nhất.
Quy trình ép phun
Với phương pháp ép phun, nhựa dạng hạt được đưa vào theo trọng lực từ phễu vào một thùng đã được gia nhiệt. Khi các hạt được đẩy chậm về phía trước bởi một pít-tông dạng vít, nhựa được ép vào một buồng đã được gia nhiệt gọi là thùng, tại đó nhựa được làm nóng chảy. Khi pít-tông tiến lên, nhựa đã được làm nóng chảy được ép qua một vòi phun nằm trên ống lót phun khuôn, cho phép nhựa đi vào khoang khuôn thông qua hệ thống cổng và ống dẫn. Khuôn duy trì ở nhiệt độ đã đặt để nhựa có thể đông lại gần như ngay khi khuôn được đổ đầy.
Chu trình ép phun
Trình tự các sự kiện trong quá trình đúc phun một bộ phận nhựa được gọi là chu kỳ đúc phun. Chu kỳ bắt đầu khi khuôn đóng lại, sau đó là quá trình phun polyme vào khoang khuôn. Sau khi khoang được lấp đầy, áp suất giữ được duy trì để bù cho sự co ngót của vật liệu. Ở bước tiếp theo, trục vít quay, đưa lần phun tiếp theo vào trục vít phía trước. Điều này khiến trục vít thụt vào khi lần phun tiếp theo được chuẩn bị. Khi bộ phận đã đủ nguội, khuôn mở ra và bộ phận được đẩy ra.
Các loại quy trình ép phun khác nhau
Mặc dù hầu hết các quy trình ép phun đều được mô tả theo quy trình thông thường ở trên, nhưng vẫn có một số biến thể ép phun quan trọng bao gồm:
- Đúc đồng phun (sandwich)
- Đúc phun lõi nóng chảy (bị mất, hòa tan)
- Đúc phun hỗ trợ khí
- Trang trí trong khuôn và cán trong khuôn
- Đúc phun nén
- Ép phun cao su silicone lỏng
- Chèn và chèn khuôn ngoài
- Khuôn ép phun dạng phiến (lớp vi mô)
- Đúc phun áp suất thấp
- Khuôn ép phun vi mô
- Khuôn đúc vi mô
- Đúc phun đa thành phần (ép khuôn)
- Ép phun nhiều lần bằng phương pháp phun trực tiếp
- Ép phun bột
- Ép phun đẩy-kéo
- Đúc phun phản ứng
- Đúc chuyển nhựa
- Đúc khuôn
- Khuôn ép phun bọt kết cấu
- Đúc phun phản ứng cấu trúc
- Khuôn đúc mỏng
- Ép phun khí rung
- Đúc phun hỗ trợ nước
- Tiêm cao su
Nhấn mạnh
Kẻ thù chính của bất kỳ bộ phận nhựa đúc phun nào là ứng suất. Khi nhựa (chứa các phân tử dài) được nấu chảy để chuẩn bị đúc, các liên kết phân tử bị phá vỡ tạm thời do nhiệt và lực cắt của máy đùn, cho phép các phân tử chảy vào khuôn. Sử dụng áp suất, nhựa được ép vào khuôn, lấp đầy mọi đặc điểm, vết nứt và khe hở của khuôn. Khi các phân tử được đẩy qua từng đặc điểm, chúng buộc phải uốn cong, quay và biến dạng để tạo thành hình dạng của bộ phận. Việc quay các góc cứng hoặc sắc gây ra nhiều ứng suất hơn cho các phân tử so với việc quay nhẹ nhàng với bán kính rộng. Các chuyển đổi đột ngột từ đặc điểm này sang đặc điểm khác cũng khó để các phân tử lấp đầy và tạo thành.
Khi vật liệu nguội đi và các liên kết phân tử liên kết lại nhựa thành dạng cứng, các ứng suất này thực chất bị khóa chặt vào bộ phận. Ứng suất của bộ phận có thể gây cong vênh, vết lõm, nứt, hỏng sớm và các vấn đề khác.
Mặc dù một số ứng suất trong một bộ phận đúc phun có thể xảy ra, bạn nên thiết kế các bộ phận của mình với sự cân nhắc nhiều nhất có thể để giảm ứng suất. Một số cách để thực hiện điều này là thêm các chuyển tiếp mượt mà giữa các tính năng và sử dụng các vòng và góc bo tròn ở các khu vực có thể có ứng suất cao.
Cổng
Mỗi thiết kế khuôn phun phải có một cổng hoặc một lỗ mở cho phép nhựa nóng chảy được phun vào khoang khuôn. Loại cổng, thiết kế và vị trí có thể ảnh hưởng đến bộ phận như đóng gói bộ phận, loại bỏ cổng hoặc vết tích, hình thức thẩm mỹ của bộ phận và kích thước và độ cong vênh của bộ phận.
Các loại cổng
Có hai loại cổng dùng cho đúc phun: cổng cắt thủ công và cổng cắt tự động.
Cổng cắt thủ công
Những loại cổng này yêu cầu người vận hành phải tách các bộ phận ra khỏi thanh trượt thủ công sau mỗi chu kỳ. Cổng cắt thủ công được chọn vì một số lý do:
- Cổng quá cồng kềnh để có thể tự động cắt bằng máy
- Các vật liệu nhạy cảm với lực cắt như PVC không thể chịu được tốc độ cắt cao
- Phân phối lưu lượng cho một số thiết kế yêu cầu phân phối lưu lượng đồng thời trên mặt trận rộng
Cổng tự động cắt tỉa
Các loại cổng này kết hợp các tính năng trong công cụ để phá vỡ hoặc cắt cổng khi công cụ mở ra để đẩy bộ phận ra. Cổng cắt tự động được sử dụng vì một số lý do:
- Tránh việc tháo dỡ cổng như một hoạt động thứ cấp, giảm chi phí
- Duy trì thời gian chu kỳ nhất quán cho tất cả các bộ phận
- Giảm thiểu vết sẹo cổng trên các bộ phận
Thiết kế cổng thông dụng
Yếu tố lớn nhất cần xem xét khi chọn loại cổng phù hợp cho ứng dụng của bạn là thiết kế cổng. Có nhiều thiết kế cổng khác nhau tùy thuộc vào kích thước và hình dạng của bộ phận của bạn. Dưới đây là bốn thiết kế cổng phổ biến:
Cổng cạnh là thiết kế cổng phổ biến nhất. Như tên gọi, cổng này nằm ở cạnh của bộ phận và phù hợp nhất với các bộ phận phẳng. Cổng cạnh lý tưởng cho các phần trung bình và dày và có thể được sử dụng trên các công cụ hai tấm nhiều khoang. Cổng này sẽ để lại vết sẹo ở đường phân khuôn.
Cổng phụ là cổng tự động cắt tỉa duy nhất trong danh sách này. Chốt đẩy là cần thiết để tự động cắt tỉa cổng này. Cổng phụ khá phổ biến và có một số biến thể như cổng chuối, cổng đường hầm và cổng mặt cười, v.v. Cổng phụ cho phép bạn cắt cổng ra khỏi đường phân khuôn, tạo sự linh hoạt hơn khi đặt cổng ở vị trí tối ưu trên chi tiết. Cổng này để lại vết sẹo có kích thước bằng chốt trên chi tiết.
Cổng đầu nóng là cổng phổ biến nhất trong tất cả các cổng đầu nóng. Cổng đầu nóng thường nằm ở phía trên cùng của chi tiết thay vì trên đường phân khuôn và lý tưởng cho các hình dạng tròn hoặc hình nón khi cần dòng chảy đồng đều. Cổng này để lại một nốt nhỏ nhô lên trên bề mặt của chi tiết. Cổng đầu nóng chỉ được sử dụng với hệ thống đúc đầu nóng. Điều này có nghĩa là, không giống như hệ thống đầu lạnh, nhựa được đẩy vào khuôn thông qua một vòi phun được làm nóng và sau đó được làm nguội đến độ dày và hình dạng thích hợp trong khuôn.
Cổng trực tiếp hoặc cổng phun là cổng được cắt thủ công được sử dụng cho khuôn khoang đơn của các bộ phận hình trụ lớn cần đổ đầy đối xứng. Cổng trực tiếp là loại dễ thiết kế nhất và có chi phí và yêu cầu bảo trì thấp. Các bộ phận có cổng trực tiếp thường ít chịu ứng suất và có độ bền cao. Cổng này để lại vết sẹo lớn trên bộ phận tại điểm tiếp xúc.
Vị trí cổng
Để tránh các vấn đề phát sinh do vị trí cổng, sau đây là một số hướng dẫn về vị trí cổng thích hợp:
- Đặt cổng ở mặt cắt ngang nặng nhất để có thể chèn một phần và giảm thiểu lỗ rỗng và độ lún.
- Giảm thiểu sự cản trở trên đường đi của dòng chảy bằng cách đặt các cổng cách xa lõi và chốt.
- Đảm bảo rằng lực tác động từ cổng sẽ không ảnh hưởng đến chức năng hoặc tính thẩm mỹ của bộ phận.
- Nếu bạn sử dụng nhựa có độ co ngót cao, bộ phận này có thể co lại gần cổng, gây ra hiện tượng “cổng nhăn” nếu có ứng suất đúc cao tại cổng.
- Đảm bảo cho phép chuyển cổng thủ công hoặc tự động dễ dàng.
- Cổng phải giảm thiểu chiều dài đường đi của dòng chảy để tránh tạo vết dòng chảy thẩm mỹ.
- Trong một số trường hợp, có thể cần phải thêm một cổng thứ hai để lấp đầy các bộ phận một cách thích hợp.
- Nếu xảy ra sự cố về độ đầy ở những bộ phận có thành mỏng, hãy thêm kênh dẫn dòng hoặc điều chỉnh độ dày thành để khắc phục tình trạng dòng chảy.
Cổng có kích thước và hình dạng khác nhau tùy thuộc vào loại nhựa được đúc và kích thước của bộ phận. Các bộ phận lớn sẽ cần cổng lớn hơn để cung cấp dòng nhựa lớn hơn nhằm rút ngắn thời gian đúc. Cổng nhỏ có vẻ ngoài đẹp hơn nhưng mất nhiều thời gian đúc hơn hoặc cần áp suất cao hơn để đổ đầy chính xác.
Độ dày của tường
Trước khi đẩy ra khỏi khuôn, các bộ phận đúc phun được làm nguội từ nhiệt độ sản xuất để chúng giữ nguyên hình dạng khi đẩy ra. Trong bước làm nguội bộ phận của quy trình đúc, cần giảm thiểu những thay đổi về áp suất, vận tốc và độ nhớt của nhựa để tránh khuyết tật. Một số khía cạnh quan trọng hơn trong giai đoạn này so với độ dày thành. Tính năng này có thể có tác động lớn đến chi phí, tốc độ sản xuất và chất lượng của các bộ phận cuối cùng.
Độ dày thành thích hợp:
Việc lựa chọn độ dày thành phù hợp cho bộ phận của bạn có thể có tác động mạnh mẽ đến chi phí và tốc độ sản xuất. Mặc dù không có giới hạn về độ dày thành, mục tiêu thường là chọn thành mỏng nhất có thể. Thành mỏng hơn sử dụng ít vật liệu hơn, giúp giảm chi phí và mất ít thời gian để làm mát hơn, giảm thời gian chu kỳ.
Độ dày thành tối thiểu có thể sử dụng phụ thuộc vào kích thước và hình dạng của bộ phận, yêu cầu về cấu trúc và hành vi chảy của nhựa. Độ dày thành của một bộ phận đúc phun thường nằm trong khoảng từ 2mm – 4mm (0,080″ – 0,160″). Đúc phun thành mỏng có thể tạo ra các thành mỏng tới 0,5mm (0,020″). Biểu đồ bên dưới hiển thị độ dày thành được khuyến nghị cho các loại nhựa đúc phun thông thường.
Độ dày thành đồng đều:
Các phần dày mất nhiều thời gian để nguội hơn các phần mỏng. Trong quá trình làm nguội, nếu thành có độ dày không đồng đều, các thành mỏng hơn sẽ nguội trước trong khi các thành dày vẫn đang đông đặc. Khi phần dày nguội đi, nó co lại xung quanh phần mỏng đã đông đặc. Điều này gây ra hiện tượng cong vênh, xoắn hoặc nứt ở nơi hai phần gặp nhau. Để tránh vấn đề này, hãy cố gắng thiết kế với các thành hoàn toàn đồng nhất trên toàn bộ bộ phận. Khi không thể có các thành đồng nhất, thì sự thay đổi độ dày phải diễn ra càng dần dần càng tốt. Sự thay đổi độ dày thành không được vượt quá 10% trong nhựa có độ co ngót khuôn cao. Sự chuyển đổi độ dày phải được thực hiện dần dần, theo thứ tự từ 3 đến 1. Sự chuyển đổi dần dần này tránh được sự tập trung ứng suất và sự khác biệt đột ngột về độ nguội.
Dấu chìm
Khi nhựa nóng chảy chảy vào khuôn ép phun, các phần dày không nguội nhanh bằng phần còn lại của chi tiết vì vật liệu dày hơn bị cách nhiệt bởi bề mặt bên ngoài của nhựa nguội nhanh hơn. Khi lõi bên trong nguội đi, nó co lại ở tốc độ khác so với lớp vỏ bên ngoài đã nguội. Sự khác biệt về tốc độ nguội này khiến phần dày bị kéo vào bên trong và tạo ra vết lõm trên bề mặt bên ngoài của chi tiết hoặc tệ hơn là làm cong vênh hoàn toàn chi tiết. Ngoài việc không đẹp mắt, vết lõm này còn biểu thị ứng suất bổ sung được tích hợp vào chi tiết. Các khu vực ít dễ thấy khác xảy ra hiện tượng lún bao gồm các gân, gờ và góc. Những khu vực này thường bị bỏ qua vì cả đặc điểm và bản thân chi tiết đều không quá dày; tuy nhiên, giao điểm của hai chi tiết này có thể là vấn đề.
Một cách để tránh vết lõm là khoét bỏ phần rắn của bộ phận để giảm các vùng dày. Nếu cần độ bền của bộ phận rắn, hãy thử sử dụng các mẫu gân chéo bên trong vùng khoét bỏ để tăng độ bền và tránh lún. Theo nguyên tắc chung, hãy đảm bảo rằng tất cả các gờ và gân định vị/gắn không quá 60% độ dày của thành danh nghĩa. Kết cấu cũng có thể được sử dụng để che các vết lõm nhỏ.
Kết cấu
Kết cấu là một quy trình được sử dụng để áp dụng các mẫu cho bề mặt khuôn. Quy trình này cho phép linh hoạt trong việc tạo ra diện mạo cuối cùng của các bộ phận của bạn. Kết cấu là một phần không thể thiếu trong quá trình phát triển sản phẩm tổng thể và nên được xem xét trong quá trình thiết kế để đạt được kết quả mong muốn. Kết cấu có thể là một thành phần chức năng của thiết kế (ví dụ, để cải thiện độ bám), cũng như là một chiến lược để ngụy trang các bộ phận không hoàn hảo hoặc được xử lý thường xuyên. Kết cấu cũng có thể được sử dụng để giảm hao mòn bộ phận do ma sát.
Có nhiều loại kết cấu khác nhau dành cho các bộ phận đúc phun như:
- Tự nhiên/Kỳ lạ
- Hoàn thiện mờ
- Hoa văn nhiều lớp bóng
- Hợp nhất
- Đồ họa
- Hạt da/Da thuộc
- Vân gỗ, đá phiến và đá cuội
- Hình học & Vải lanh
- Kết cấu nhiều lớp để tạo ra diện mạo mới
- Hình ảnh hoặc Logo được kết hợp vào mẫu
Khi áp dụng kết cấu cho một bộ phận, bản vẽ CAD phải được điều chỉnh để phù hợp với sự thay đổi bề mặt này. Nếu kết cấu nằm trên bề mặt vuông góc hoặc nghiêng ra khỏi lỗ khuôn, thì không cần thay đổi độ dốc. Tuy nhiên, nếu kết cấu nằm trên bề mặt song song với lỗ khuôn, thì cần tăng độ dốc để tránh trầy xước và vết kéo có thể xảy ra trong quá trình đẩy bộ phận ra. Các kết cấu khác nhau có tác động khác nhau đến bộ phận được đúc. Nguyên tắc chung khi thiết kế kết cấu là có 1,5 độ dốc cho mỗi 0,001″ độ sâu hoàn thiện kết cấu.
Đường phân chia
Đường phân khuôn là đường phân chia trên chi tiết nơi hai nửa khuôn gặp nhau. Đường này thực sự chỉ ra “mặt phẳng” phân khuôn đi qua chi tiết. Trong khi trên các chi tiết đơn giản, mặt phẳng này có thể là một bề mặt phẳng đơn giản, thì nó thường là một hình dạng phức tạp, vạch theo chu vi của chi tiết xung quanh các đặc điểm khác nhau tạo nên hình bóng bên ngoài của chi tiết. Đường phân khuôn cũng có thể xuất hiện ở nơi bất kỳ hai mảnh khuôn nào gặp nhau. Điều này có thể bao gồm chốt tác động bên, chèn dụng cụ và van ngắt. Không thể tránh khỏi đường phân khuôn; mọi chi tiết đều có chúng. Hãy nhớ rằng khi thiết kế chi tiết của bạn, chất nóng chảy sẽ luôn chảy về phía đường phân khuôn vì đây là nơi dễ thoát khí bị dịch chuyển nhất.
Các lỗi đúc khuôn phổ biến
Ép phun là một công nghệ phức tạp với các vấn đề sản xuất có thể xảy ra. Chúng có thể do lỗi trong khuôn hoặc thường xuyên hơn là do gia công chi tiết (đúc).
Hãy ghi nhớ những yếu tố này khi thiết kế bộ phận đúc phun của bạn và nhớ rằng tránh các vấn đề ngay từ đầu sẽ dễ hơn là thay đổi thiết kế sau này.
Lỗi khuôn mẫu | Tên thay thế | Mô tả | Nguyên nhân |
Mụn rộp | Phồng rộp | Vùng nhô lên hoặc có lớp trên bề mặt của bộ phận nhựa | Dụng cụ hoặc vật liệu quá nóng, thường là do thiếu hệ thống làm mát xung quanh dụng cụ hoặc bộ phận gia nhiệt bị lỗi. |
Vết cháy | Bỏng không khí/bỏng khí | Các vùng bị cháy đen hoặc nâu trên phần nhựa nằm ở những điểm xa nhất tính từ cổng | Dụng cụ thiếu lỗ thông hơi, tốc độ phun quá cao. |
Vệt màu (Mỹ) | Thay đổi màu cục bộ | Vật liệu nhựa và chất tạo màu không được trộn đều, hoặc vật liệu đã hết và bắt đầu chỉ còn màu tự nhiên. | |
Tách lớp | Các lớp mỏng giống như mica được hình thành ở một phần tường | Sự nhiễm bẩn của vật liệu ví dụ như PP trộn với ABS; rất nguy hiểm nếu bộ phận được sử dụng cho ứng dụng quan trọng về an toàn. Vật liệu có rất ít độ bền khi bị tách lớp vì các vật liệu không thể liên kết. | |
Đèn nháy | Gờ | Vật liệu thừa trong lớp mỏng vượt quá hình dạng bình thường của bộ phận | Hư hỏng dụng cụ, tốc độ phun/vật liệu phun quá cao, lực kẹp quá thấp. Cũng có thể do bụi bẩn và chất gây ô nhiễm xung quanh bề mặt dụng cụ. |
Nhúng chất gây ô nhiễm | Các hạt nhúng | Hạt lạ (vật liệu bị cháy hoặc vật liệu khác) được nhúng trong bộ phận | Các hạt trên bề mặt dụng cụ; vật liệu bị nhiễm bẩn hoặc mảnh vụn lạ trong nòng súng; hoặc nhiệt cắt quá lớn làm cháy vật liệu trước khi phun. |
Dấu hiệu dòng chảy | Dòng chảy | Các đường hoặc hoa văn lượn sóng “lệch tông” theo hướng | Tốc độ phun quá chậm (nhựa đã nguội quá nhiều trong quá trình phun; tốc độ phun phải được thiết lập ở mức nhanh nhất có thể. |
Phun nước | Phần bị biến dạng do dòng vật liệu chảy hỗn loạn | Thiết kế dụng cụ, vị trí cổng hoặc thanh dẫn kém. Tốc độ phun được đặt quá cao. | |
Sự phân hủy polyme | Sự phân hủy polyme do oxy hóa, v.v. | Nước dư thừa trong hạt, nhiệt độ trong thùng quá cao | |
Dấu chìm | Trầm cảm cục bộ (Ở vùng dày hơn) |
Thời gian giữ/áp suất quá thấp, thời gian làm mát quá ngắn; đối với ống dẫn nóng không có vòi phun, nguyên nhân cũng có thể là do nhiệt độ cổng được đặt quá cao. | |
Cú đánh ngắn | Khuôn không điền đầy/khuôn ngắn | Một phần | Thiếu vật liệu; tốc độ phun hoặc áp suất quá thấp. |
Dấu vết nứt | Vết bắn tung tóe/vệt bạc | Hoa văn tròn xung quanh cổng do khí nóng gây ra | Độ ẩm trong vật liệu, thường xảy ra khi nhựa được sấy khô không đúng cách. |
Độ dai | Xâu chuỗi | Những phần còn lại giống như sợi dây từ cú đánh trước đó được chuyển sang cú đánh mới | Nhiệt độ vòi phun quá cao. Cổng phun chưa đóng băng. |
Khoảng trống | Khoảng trống bên trong một phần (túi khí) |
Thiếu áp suất giữ (áp suất giữ được sử dụng để đóng gói bộ phận trong thời gian giữ). Ngoài ra, khuôn có thể không khớp (khi hai nửa không nằm đúng vị trí và thành bộ phận không có cùng độ dày). | |
Đường hàn | Đường đan/đường đan xen | Đường đổi màu nơi hai mặt trận dòng chảy gặp nhau | Nhiệt độ khuôn/vật liệu được đặt quá thấp (vật liệu lạnh khi tiếp xúc với nhau nên không liên kết được). |
cong vênh | Phần xoắn | Phần bị méo mó | Thời gian làm mát quá ngắn; vật liệu quá nóng; thiếu khả năng làm mát xung quanh dụng cụ; nhiệt độ nước không chính xác (các bộ phận cong vào phía nóng của dụng cụ). |
CÔNG TY CỔ PHẦN ĐẦU TƯ THƯƠNG MẠI IMART
Mọi thắc mắc quý khách vui lòng liên hệ tới chúng tôi thông qua thông tin bên dưới hoặc quý khách có thể điền thông tin ở form bên cạnh. Chúng tôi sẽ liên hệ giải đáp thắc mắc tới quý khách một cách sớm nhất.
- Địa chỉ: 130 Cao Đức Lân, Phường An Phú, Tp Thủ Đức, TP.HCM
- Kho hàng: số 02, đường 43, Kp 5, P. An Phú, Tp Thủ Đức, Tp HCM
- Nhà xưởng: Khu đồi dù, 114 Thái Bình 2, P. Long Bình, Tp Thủ Đức, Tp HCM
- Email: [email protected] – [email protected]
- Điện thoại: 0909 653337 – 0901 846 123
- Website: https://plasticsaigoncom
- Website 2: https://imart.com.vn/